Which Positive Displacement Pumps Are Best for Corrosive Chemicals?
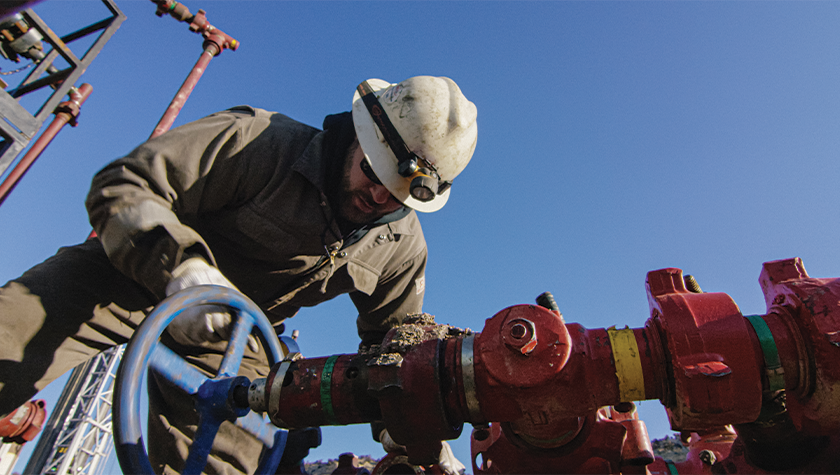
WHICH POSITIVE DISPLACEMENT PUMPS ARE BEST FOR CORROSIVE CHEMICALS?
Anyone who has tried using an ordinary pump to handle corrosive fluids knows things can get real ugly real fast. That’s why it’s important to choose a pump that is fit for purpose and will stand up to the extra wear and tear in a harsh chemical environment. Choosing the right supplier can make a massive difference in the life of your pump.
There are some key considerations when choosing the best positive displacement pumps for corrosive chemicals. Some are obvious. Others are not.
Below, we’ll profile two of the top-selling progressive cavity pumps for harsh chemical applications.
Why a positive displacement pump?
Positive displacement (PD) pumps are well suited to both chemical transfer and blending (dosing), which covers the majority of applications involving corrosive liquids.
They are the preferred choice for handling harsh chemicals because you can be confident that what goes into the pump will go out. In dosing applications, you can be assured all of the chemicals are getting where it needs to go. Plus, nothing is left sitting inside the pump where it can cause damage.
Built with components designed to stand up to harsh chemicals
Naturally, when choosing a pump for use in corrosive environments, any components that come into contact with the chemical will need to be chemical-compatible. This includes the pump body, rotors, seals, and rotors.
In most situations, stainless steel components are recommended (pump body and rotors). Among the notable exceptions are chemicals like sulphuric acid, where industrial-grade plastic components are more suitable. Seals come in a variety of advanced elastomers, which can stand up to a wide range of chemical tolerances.
Some chemicals are harder on seals than others. If this is a concern, pumps like the Waukesha Cherry-Burrell (Universal Series) can be configured with an optional flush system.
A small line attached to a water source will clean the seal as the pump runs. This prevents chemicals from settling on the seal and hardening, which can quickly lead to cracking. Waukesha’s Universal Series of stainless PD pumps is known for tight tolerances between the pump body and rotors and provides exceptional performance at a great value.
Positive displacement pumps for handling corrosive viscous fluids
Positive displacement pumps are generally well suited to managing viscous fluids. For example, the Waukesha Universal Series PD pumps can handle viscosities up to 1,000,000 centiPoise (cps). They are also built to work with fluids containing high or low pH chemicals.
Peristaltic pumps are a type of positive displacement pump that incorporates a hose and roller systems to move viscous fluids in either direction. Brands such as those manufactured by FlowMotion Systems are widely used for applications involving acids and slurries. A common use in the oil & gas and mining sectors involves reclamation in tailings ponds.
Extending your pump life
How long will a pump last? It’s impossible to say, as there are so many factors involved: fluid type, operating specifications, continuous run-time, etc.
It goes without saying that pumps used to move harsh chemicals require extra care and attention. You can save yourself a whole lot of grief and a fair chunk of change if your supplier is set up to repair and service your pump.
A full-service supplier will be able to provide you with all of the parts you need and have wearable parts readily available when you’re in a pinch. At Jadler, we advise our clients to maintain a small stock of seals and other consumables.
Ideally, your supplier will provide the training for your field staff to replace wearable components – saving you the time and expense of calling in a service team.
Reconditioning and rebuilding
Even the best-built pump will require the services of a trained expert to conduct more extensive repairs. It’s a huge advantage to work with a supplier that’s set up to support you throughout all stages of your pump life. Especially if your pump is dealing with the added strain that comes with handling challenging fluids.
Jadler is a factory-certified repair shop for key manufacturers such as Waukesha Cherry-Burrell and Walchem Chemical Metering Pumps. We are able to diagnose and rebuild equipment to meet factory specifications on our test bench. This allows our customers to extend pump service life and maintain a high level of performance.
Choosing a pump for your application
As with any pump, an experienced supplier will work with you to recommend the best pump for your application. They’ll help you determine the best option for the chemicals you’re using, and ensure it’s the right size and configuration based on your operating specs.
Top-selling positive displacement pumps for corrosive chemicals:
1. SPX Flow Waukesha Cherry-Burrell (Universal Series 1, 2 and 3)
- What Makes This Pump Great? A workhorse for handling high or low viscosity fluids.
- Common Fluid/ Chemical Applications: Thick or Viscous Fluids, solvents, polymers, lubricants, and slurries.
- Low Viscosity Applications: Rotors, made of Waukesha “88” alloy, can be run with close clearance to the 316L stainless steel fluid head without galling or seizing should inadvertent pressure surges cause contact. The close clearances combined with the rotor geometry, which gives a long sealing path between the pump inlet and outlet, allow low slip operation. As a result, you achieve high efficiency, good priming ability, metering capability, and good flow control.
- High Viscosity Applications: The large fluid cavities of the rotors, plus the large, easy entry anti-cavitation ports, allow efficient pumping of high viscosity fluids, slurries or even liquids with large chunks or particles.
- Pump Volume: Up to 500 GPM
- Operating Pressure: Up to 450 PSI
- Fluid Viscosity: Up to 1,000,000 cps
2. FlowMotion Systems Peristaltic Pumps
- What Makes This Pump Great? Self-priming, high capacity and can be run dry without damage.
- Common Fluid/Chemical Applications: Chemical transfer or chemical injection
- Pump Volume: Up to 130 GPM with suction lift of 30 feet.
- Operating Pressure: Up to 218 PSI
- Fluid Viscosity: Up to 100,000 cps