Tips on Designing an Acid and Disinfection System for Livestock Water Supply
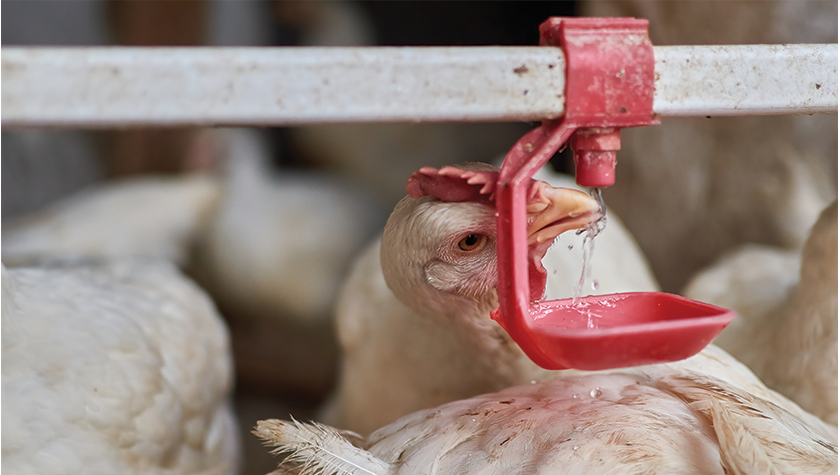
TIPS ON DESIGNING AN ACID AND DISINFECTION SYSTEM FOR LIVESTOCK WATER SUPPLY
Research shows that when livestock has an adequate supply of high-quality water, they drink more, eat more and experience more rapid weight gain. In addition, they are less prone to disease and experience fewer health problems.
The two most common challenges commercial chicken and hog producers face involve maintaining consistent pH levels and treating water for harmful pathogens such as bacteria, algae and other contaminants.
Both of these concerns can be easily managed by installing the proper chemical injection system to regulate the process. (There’s also nutrient injection, but we’ll cover that as a separate topic.)
There are a few basic issues you need to be aware of before sourcing equipment and building a system. We’ve found there is a ‘clean’ and effective way to build these systems and are pleased to share our best practice recommendations.
Design your acid dosing system around a pH setpoint vs flow rate
Most of the hog and chicken producers we work with have been advised by their veterinarians to aim for pH levels in the range of 5.5 to 6.0 range. This can be achieved by injecting a mild acid into the water.
While it may seem logical to regulate pH chemical dosage based on flow rate, this doesn’t work with livestock. There is a large disparity between what a newborn chick can consume versus an 8-week-old broiler. So, the flow rate is not an ideal measurement. The other challenge is that it is difficult to calculate dosage per unit of water in order to achieve a target pH point. It is much easier to set the dose by using a sensor.
Instead, we advise clients to manage their dosing around a pH setpoint. This is easily achieved by choosing a pump with a proportional control system, such as the Walchem W600 i/o Water Treatment Controller.
The W600 allows for multiple sensor inputs, as well as multiple analog (4-20 mA) inputs and outputs (for example: pH, level, water temperature conductivity). A sensor can be placed 10’ to 20’ from the injection point to provide an accurate measurement of pH.
Walchem’s W600 also enables proportional pulse control, so the pump can be controlled according to pump strokes, based on the setpoint. The pump speed will slow the closer it gets to the set point. This helps protect against injecting too much chemical… which is costly and can harm the animal.
Proportional control also allows for variable rates of flow volume.
What you need to know about injecting disinfectant
In any commercial livestock system for dispensing drinking water, it’s crucial to guard against harmful bacteria and algae that can form in the water lines. Typically, it involves using a disinfectant such as chlorine bleach or hydrogen peroxide.
One important thing to remember when working with disinfectants is that they require 30 to 60 minutes of contact time (‘residence time’) to be effective.
The most common sensor for injecting disinfectant is an ORP (oxidization reduction potential) sensor. This sensor provides a proxy measurement that can be compared against a titrate test to corelate the value between your ORP and free chlorine/peroxide levels and adjust the injection levels accordingly.
You will need to conduct a titrate test every few days, because conditions can fluctuate due to water temperate changes. Other factors to consider are seasonality and the water source.
The big advantage is that ORP sensor allow you to easily adjust pump settings on the fly to adjust for this fluctuation.
We generally do not recommend chlorine sensors, as they can be quite expensive and are harder to maintain.
What is the best pump for injecting disinfectant?
The Walchem E-Series provides a durable, high-quality solution at a cost-effective price. It is available in a number of models and configurations based on your setup and operational specifications. Plus, it is compatible with the Walchem W600, allowing for coordinated acid and disinfectant injection.
Jadler Pro Tip: Inject the acid before the disinfectant
When setting up an acid/disinfectant system, we advise injecting the acid before the disinfectant. Disinfectants are more effective at a lower pH level.
Sizing your chemical injection pump
There are a number of factors that will determine your pump size. Jadler will ask the following questions before making a recommendation:
- What are your water flow rates?
- What is your operating pressure?
- What chemicals are being used?
- What are the concentrations?
- What is the incoming and target pH?
- What is your target disinfection level (ppm)?
- What are your chemical compatibility challenges? (eg. PVC, copper pipe)
Once we have the answers to these questions, we can size and price an all-in solution that includes pumps, sensors and valves.
Don’t overcomplicate things
There are a number of ways to tackle the challenge of acid and disinfection injection for livestock water supply. At Jadler, we have developed a straightforward, turnkey solution that has proven itself to deliver the best performance and the best possible value. Time and time again. Contact us and we’d be happy to recommend the right solution for your livestock operation.