Alcohol Auto-Cut and Blending Systems
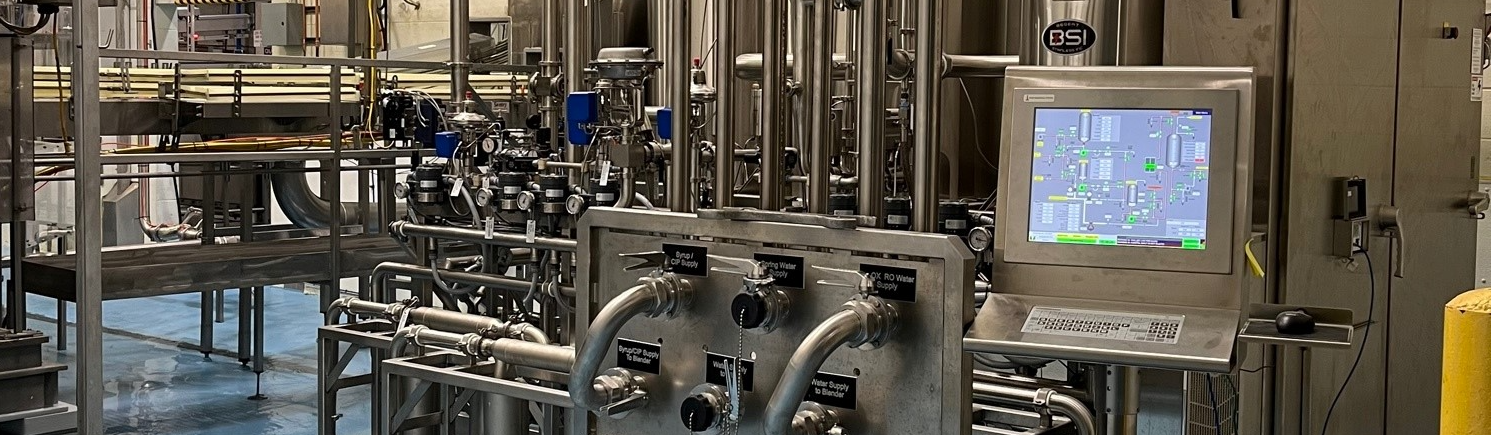
Client
National 'White Label' Beverage Company
Industry
Food & Beverage
JADLER SERVICES
Sanitary Tig Welding & Fabrication, Installation, Instrumentation, Equipment Supply/Removal, General Contracting
PRODUCT LINES
Waukesha Cherry-Burrell (SPX Flow), APV (SPX Flow), GEA Tuchenhagen, Fristam Pumps, Endress + Hauser
THE CHALLENGE
To meet the skyrocketing demand for alcoholic seltzers and similar products, Canada’s largest beverage company contracted Jadler’s team of sanitary equipment specialists to install two key systems to optimize the production of RTD beverages: an alcohol auto-cut system and a product blending system.
THE SOLUTION
As production volume increased, our client wanted to improve margins by auto-blending the alcohol themselves.
This would involve the construction and installation of:
- An outdoor Class 1, Division 1 receiving tank and piping (rated for flammable/ explosive liquids)
- A blender to precisely dilute the alcohol to 19.5% with distilled water (RO)
- Inside storage tanks for the blended alcohol
- All product piping (alcohol, syrups, nitrogen, CO2, air) and hangers
- All required valves (proof, butterfly, check), flow meters, level switches, levels transmitters, pressure gauges and transmitters, inline mixers, tube and fittings and hoses
- Tie-in to CIP supply and return
- Fabrication of stainless frames and catwalks
As the designated Process Mechanical Contractor for the project, we subcontracted the nitrogen piping and mechanical air piping work, oversaw the electricians, brought in a rigging specialist and hired a structural engineer to design the hanger supports. It proved to be the perfect mix of skills and expertise.
Both projects were completed on schedule, allowing our client to ramp up production ahead of the busy summer season. The system is working as designed and has dramatically improved plant efficiency and profitability.
.
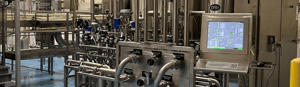