Magmeter Installation and Calibration Best Practices
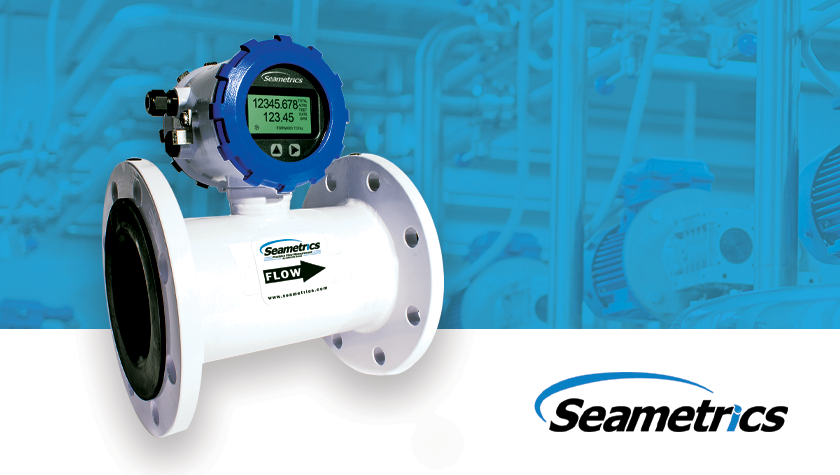
Electromagnetic Flow Meters (magmeters) use electromagnetic induction to determine the flow rates of conductive liquids in pipes.
To ensure consistently accurate readings, they must be correctly installed. This involves more care and attention than other, more common flow meters. However, by following these installation best practices, you can ensure your Magmeter provides years of reliable service.
Note: These are meant to be general guidelines. Every model and brand will have specific recommendations. When installing or calibrating a magmeter, always follow the manufacturer’s instructions outlined in the product manual. Or contact an experienced installer to do it on your behalf.
START BY CHOOSING THE RIGHT MAGMETER
There are several factors to consider when choosing a Magmeter for your specific application.
- Brand: Reputable and well-established brands have a proven track record of providing consistently accurate measurements.
- Operational Conditions: It’s crucial that you know your operating temperature and pressures. If the magmeter is not rated for your operating parameters, it can significantly reduce the meter’s product life.
- Fluid Type: The type of fluid will impact your choice of magmeter. For example, magmeters used for viscous fluids, acids, or corrosive liquids contain built-to-purpose components to ensure safe handling and long product life. Maqmeters also need the fluid to be conductive.
- Particulate Bubbles: Lastly, if there are particulates and bubbles in the fluid then you may require air eliminators or filters to improve the accuracy of your readings.
PROPER MAGMETER INSTALLATION
1. Recommended Magmeter Placement.
When determining the placement of a Magmeter, there are three key considerations:
- Straight Pipe Length: Install the magmeter with a recommended length of straight pipe (upstream AND downstream). Typically, it’s about two (2) pipe diameters length upstream and one (1) pipe diameters length downstream from any bends, valves, or other disturbances. This ensures a uniform flow profile.
- Avoid Air Pockets: Position the magmeter in a location where the pipe is full of liquid at all times. For horizontal pipes, we suggest placing the meter slightly below the highest point.
- Access: To make things easy on yourself, try to select a spot that is readily accessible for future maintenance, calibration, and troubleshooting.
2. Avoid equipment that produces electrical interference.
Because it monitors electromagnetic currents, any electrical interference can impact readings. Avoid installing your magmeter near large motors, transformers, or other equipment that generates strong electromagnetic fields.
3. ENSURE IT’S PROPERLY WIRED & GROUNDED
Another way to reduce interference is to use shielded cables for all signal wiring. Whenever working with instrumentation for liquids processing, connections should be secure and sealed to keep moisture out.
Of course, properly ground your Magmeter to prevent electrical noise and interference further. Refer to the grounding instructions provided by the manufacturer. The use of grounding rings is key with non-metal pipe material and in some cases use of earth ground is required.
4. PAY ATTENTION TO THE FLANGE CONNECTION
As always, you’ll need to ensure all flange surfaces are clean with no signs of damage before connecting and using the gaskets recommended by the manufacturer.
DO I NEED TO CALIBRATE MY MAGMETER?
Magmeters don’t have any moving parts that can wear out like mechanical-style meters. However, magmeters can, over time, “drift”. Depending on the application, it’s recommended to perform a “flow test” on your magmeter every 12 months.
1. CHOOSE YOUR CALIBRATION METHOD
There are two different methods you can use to calibrate your Magmeter:
Comparison Method/Master Meter: Compares the readings with another flowmeter that has been recently calibrated. This will allow you to compare flow rates to determine if your magmeter is still within spec. Like watches, no two meters will be 100% the same but should be within 0-5% to 2%.
Volumetric Method: Measures the fluid volume passed over a specific time and compares it to the magmeter reading.
2. PERFORM THE CALIBRATION
As soon as you start the flow, record the reading from the magmeter. At the same time, record the reading from the reference instrument (for the volumetric and gravimetric methods, this will involve the volume/weight of fluid).
3. COMPARE READINGS
Compare the two readings and calculate the margin of error between the magmeter reading and the reference reading. This will give you an idea of the accuracy of your magmeter. If it’s determined that the meter is no longer within the specified accuracy then you’ll need to decide if the meter should be replaced or sent back to the factory for a proper calibration.
4. RECORD THE RESULTS
Always document the calibration results – including any adjustments made and other relevant observations. This provides a history of the meter’s performance and ensures traceability, which may help with future calibration.
HOW OFTEN DO YOU NEED TO RECALIBRATE?
Every manufacturer will provide guidelines on when to recalibrate the equipment. That said, your unique operating conditions and the required level of accuracy in your application will determine how often to recalibrate your magmeter. Regulatory requirements may require more frequent equipment calibration where more precise measurement is crucial.