Do I Need an Ultrasonic or Radar Level Sensor for My Tank Application?
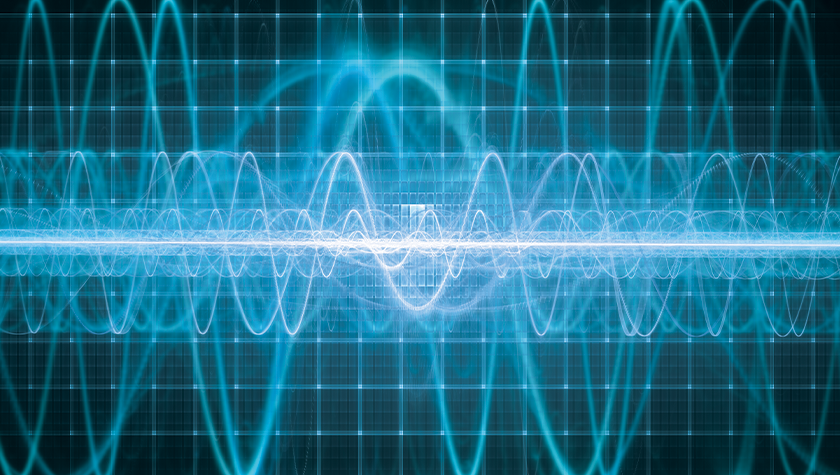
DO I NEED AN ULTRASONIC OR RADAR LEVEL SENSOR FOR MY TANK APPLICATION?
Choosing the right non-contact continuous level sensor for your fluid application should be relatively easy. After all, if the plan is to avoid contact with the fluid, it generally comes down to one of two options: Ultrasonic or Radar. Ultrasonic sensors are available at a low cost and generally allow for easy setup. However, several factors will determine which option is right for you.
4 factors will determine whether you require an ultrasonic or radar level sensor:
- Process conditions (eg. basic, steam, vapor or foam)
- Tanks size and configuration
- Tank anomalies and process connections (eg. an agitator, baffle, tank risers or heat coil)
- Open or closed tank
Continue reading or jump down to our Ultrasonic vs. Radar Level Sensor Comparison Chart.
How Ultrasonic and Radar Level sensors work
Both sensors are designed to sit above the fluid. They’re contactless. Each transmits waves that reflect off the surface of the fluid. By performing some simple calculations, they can measure the fluid level inside the tank.
Ultrasonic sensors emit sound waves, while radar deploys electromagnetic waves (radio microwaves).
There are crucial differences between the two types of waves.
Unlike sound waves, electromagnetic waves don’t need to travel through a specific medium (eg. air). If a fluid does not reflect sound, you will require a radar sensor. Radar sensors can even operate in a vacuum. These properties make radar sensors better suited to several challenging processes and tank configurations.
Also, since radar isn’t affected by fluctuations in the medium, it is more accurate. Even small variations can impact the speed of sound waves, skewing the measurement.
As you’ll see, these wave characteristics impact where each technology will excel.
1. Choosing a level sensor: Process conditions
Ultrasonic Sensors:
An ultrasonic sensor is the economical choice if you’re working with basic fluids in a general or intrinsically safe application. This could include water, wastewater, fuel, lighter oils and less-viscous fluids. Note: Temperature changes can reduce accuracy, and noisy environments can interfere with sound waves and affect readings.
Radar sensors:
Radar sensors can accurately measure a wider range of fluids. They stand out in applications where the medium is inconsistent, and the process may result in physical interference. This includes processes involving:
- Gas (steam, vapor, condensation)
- Foam
- Viscous fluids
- High or fluctuating temperatures
- Pressurized tanks
- Vacuums
- Noise
- Dust
2. Choosing a level sensor: Tank type
The size, shape and construction of your tank will influence which type of sensor works best and may dictate where your sensor should be positioned.
Tank material
Both sensors will generally work in any tank regardless of the material. Radio microwaves (radar) can penetrate the tank if it is made of a non-conductive material (such as fiberglass, glass or polyethylene). This gives you the option of mounting a radar sensor above the vessel for greater ease of installation.
Tank size
Either sensor will function in larger tanks with longer-range level measurements. For example, Flowline™ UG series ultrasonic sensors have a range of 4.9’ to 39.3’ (1.5-12 m). That said, radar sensors are often the preferred choice due to the limitations of ultrasonic sensors:
- Ultrasonic sensors require a larger opening on the tank ceiling.
- Also, ultrasonic sensors have a blind spot “dead band” where they cannot conduct a reading. In larger tanks, this can be over 3’. Radar sensors can measure right up to the top of the tank with no issue.
Both provide comparable accuracy in small vessels. This was once the domain of ultrasonic sensors, but improvements in radar sensor signaling have changed this.
Domed Tanks
Where you mount the sensor in a dome tank is extremely important. If the port is in the middle of the tank you will need to use a radar sensor, as an ultrasonic sensor cannot be installed in the middle of the dome.
3. Choosing a level sensor: Tank anomalies
Your tank may be fitted with various process elements such as an agitator, baffles or heating coils. An ultrasonic sensor often can’t determine if it is reflecting off a process element or the fluid. This inability to differentiate can result in an inaccurate reading. In many cases, this can be avoided through careful sensor placement.
This is generally not a problem with radar sensors. That’s because electromagnetic waves have a narrower beam angle that can bypass the tank’s obstructions to avoid false readings. Also, Flowline’s Radar Sensors have a false echo curve feature – allowing you to “map” the tank when it’s empty and ignore false return signals.
Additionally, a radar sensor can be mounted on a tank riser and situated closer to the sidewall if necessary. This gives you greater flexibility to install in a position where interference will not be an issue.
4. Choosing a level sensor: Open or closed tank
Both level sensor types are commonly used in closed or open tanks in an indoor setting. Ultrasonic sensors are not ideal for open tanks in outdoor environments, because wind and debris can interfere with the sound waves. This is not a concern with a radar sensor.
Ultrasonic vs. Radar Level Sensor Comparison Chart
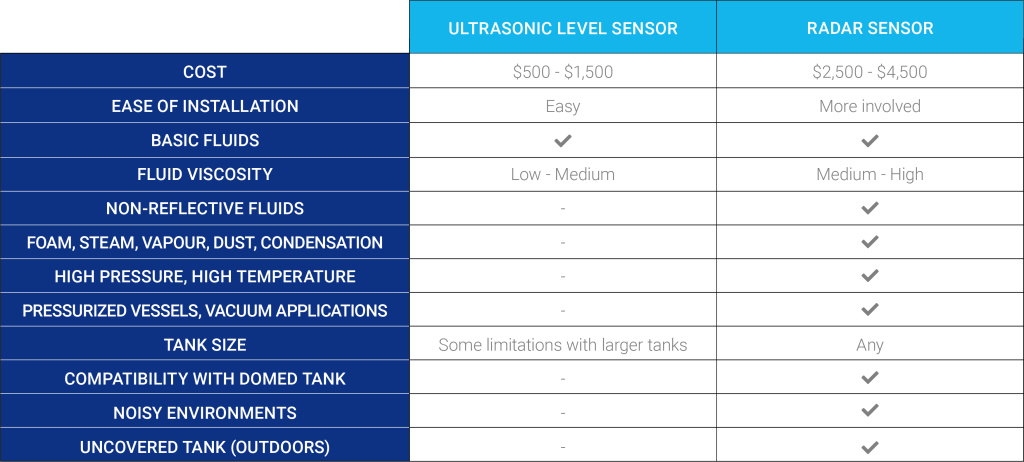
Explore Jadler’s Line of Level Sensors by Flowline™
Whether you require an ultrasonic or radar level sensor, Jadler is pleased to carry a complete offering of products by Flowline™. Flowline is known for dependable, long-lasting, high-quality products at a competitive price.
All Flowline sensors come with a standard 4-20 mA output. Flowline’s LR36 Sensor has a PTFE inner shield for corrosive environments. They also offer radar sensors for a range of specialized applications, including lift stations, agitation, open tanks and solids.
Because Flowline products are manufactured in California, not overseas, delivery and distribution are never a concern. Jadler maintains a healthy inventory of Flowline’s top-selling sensors. If you require a non-stocked or custom order, we can typically get it in less than four weeks.